How to cleverly remove the most common disturbing yarn faults
Clever yarn clearing is profitable, efficient and easy. Profitability and efficiency go hand in hand and are based on avoiding unnecessary interventions in the running process. To ensure quality outputs, only a precise removal of disturbing faults should occur, allowing the required quality goals to be met. To achieve this, the yarn quality control system needs to be clever in the execution of its task while being easy to handle. Welcome to YarnMaster® PRISMA - delivering the most efficient NSLT clearing.
It’s worth looking into the removal of the most common faults in staple fiber yarns, such as neps, thick and thin places and long faults, that cause most of the cuts in the yarn clearing process.
Based on correct fault detection and classification, and a precise cutting execution, PRISMA offers many advantages in NSLT clearing:
- Most efficient NSLT clearing based on clever simultaneous dual measurement
- Highly customizable through a fully flexible setting curve, with up to 24 possible setting points, which can be inserted and moved by touch
- Easy and intuitive operation with visual curve set by drag and drop
- Clear information to optimize the production process with the most detailed fault classification and Scatter Plot view
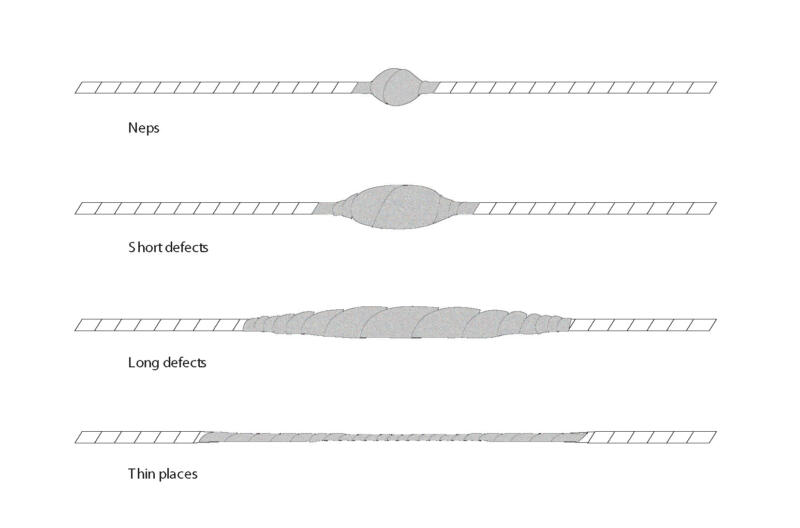
Most efficient NSLT clearing
NSLT faults can be categorized into four groups: Neps, thick places, thin places, and long faults (thick). These faults are the most common and thus cause most of the cuts during yarn clearing.
Because NSLT faults can be disturbing, the used quality control system must perform its task accurately to ensure the yarn quality, while keeping the winding machine efficiency high. So even the most basic fault removal depends on the measurement technology and its signal-processing software to achieve:
- Correct fault detection
- Correct fault classification
- Correct cut execution
- No unnecessary cuts
By default, PRISMA employs its optical infrared and mass sensors to monitor NSLT faults with the utmost precision. This dual measurement technique guarantees that 100% of the yarn is always double-checked, ensuring correct fault detection. Combined with the NSLT clearing software, correct fault classification and cut execution are given - ensuring profitability and quality.
NSLT source of origin
There are many origins of NSLT faults. A general rule is that the shorter the defect, the later it occurred in the spinning mill. This is also due to the drafting of the various machines in the spinning mill. To get to the bottom of possible causes of faults, Loepfe has been providing this information table Classification of yarn faults and their sources. The chart supports the operators in the efficient elimination of causes and thus makes a significant contribution to increasing quality and winding machine efficiency.
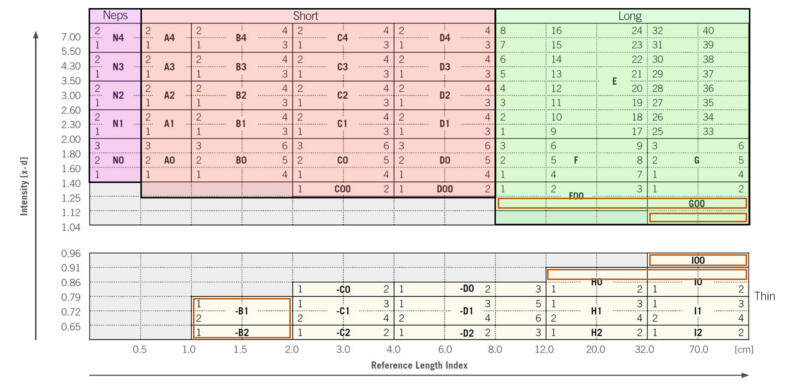
Easy NSLT clearing
PRISMA provides a high level of customizability if required. With up to 24 possible setting points, the NSLT clearing matrix can be tailored to meet the specific needs of the production process. The intuitive drag-and-drop interface makes it easy to set the curves, giving complete control over the clearing and classification process. (Setting tutorial: Visual creation of clearing curve) The system also offers a very fine classification, providing precise numbers for classified yarn defects and events in the unique classes F00, G00, I00, H0, I0 and -B1, -B2.
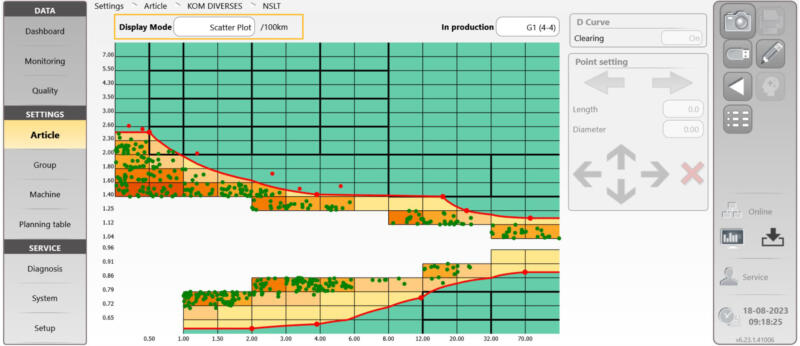
The fault distribution chart "Scatter Plot" visualizes, with different colors, cut yarn faults and events below the curve. This makes it easy to optimize and understand yarn quality, allowing informed decisions about the production process.
Classification of NSLT faults
Thick and thin places:
- Whether there is an increase or a decrease in diameter compared to the average yarn diameter
Within the thick places, a further distinction is made:
- Neps, as extremely short and extremely thick defects (up to 0.4 cm)
- Short defects, as defects of a limited length (from 0.5 to 8 cm) but of considerable thickness
- Long defects and double threads, as defects of considerable length (from 8 to 128 cm) but of limited thickness
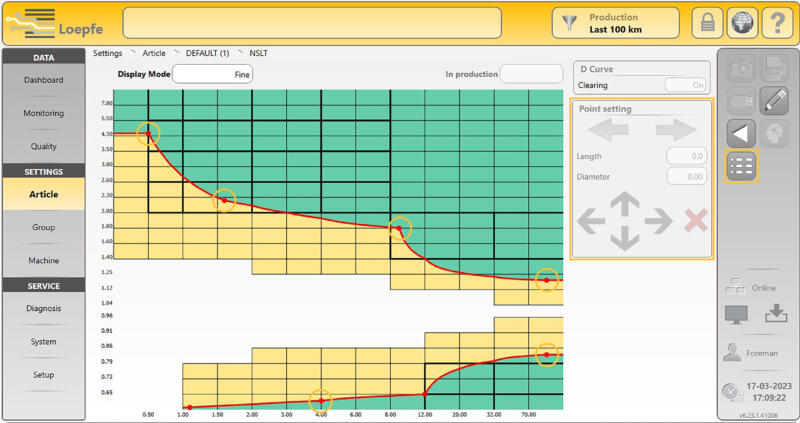
NSLT Matrix
Setting points (marked with the yellow circles) are introduced to plot the clearing curve. A maximum of 16 points are available for the NSL curve and 8 points for the thin curve, offering 24 possible setting points for maximum customizability.
The setting point coordinates can be entered directly under the coordinates table or the individual points can be changed in the matrix via the touch function, or with the help of the point setting field.
Most efficient basic yarn clearing
The YarnMaster® PRISMA system - the ultimate solution for removing unwanted yarn characteristics with maximum efficiency. Designed to support Loepfe users in achieving their profitability and quality goals, PRISMA combines state-of-the-art technology and innovative software to deliver unparalleled yarn clearing capabilities.
With its advanced features, the PRISMA system ensures that every strand of yarn meets the highest standards of quality and performance. Through dual measurement and the NSLT cluster feature, this system provides the most efficient basic yarn clearing solution on the market.