Transfer of product portfolio WeftMaster® to PROTECHNA
Transfer of product portfolio WeftMaster® to PROTECHNA
Loepfe announces a significant strategic decision aimed at enhancing efficiency and customer service. Starting January 1, 2025, the entire WeftMaster® product portfolio will be transferred to Loepfe's sister company PROTECHNA. This move is designed to leverage synergies within the Vandewiele Group and deliver even more comprehensive solutions in yarn-clearing and fabric quality to valued customers.
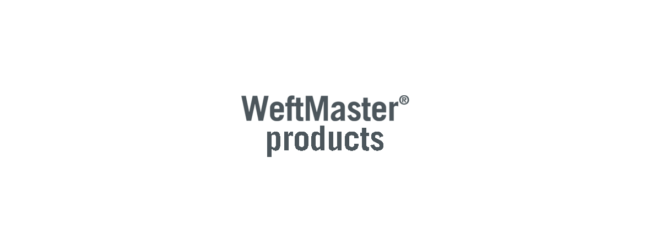
As of January 1, 2025, the entire product portfolio of Loepfe's WeftMaster® division will be transferred to their sister company PROTECHNA. The decision had been made in order to better leverage synergies within the Vandewiele Group and to further improve customer service.
PROTECHNA is an established producer of high-quality thread and fabric control systems for various textile manufacturing processes. Acquiring Loepfe WeftMaster® products will ideally complement PROTECHNA's existing product portfolio and offer mutual customers comprehensive and innovative solutions for the control of thread and fabric quality.
The transfer will allow Loepfe to focus more on the core business and drive innovation forward. This measure will enable Loepfe also, to strengthen the market position sustainably and offer customers improved yarn-clearing solutions for winding machines, rotor spinning machines, and air-jet spinning machines in the field of staple yarn spinning. This strategic realignment will be beneficial for mutual customers and for both companies in the long term.
Until December 31, 2024, Loepfe Brothers Ltd. would remain the point of contact for the WeftMaster® product line, after which PROTECHNA would handle all requests starting January 1, 2025.