MillMaster ”Planning board” profitability trough optimization
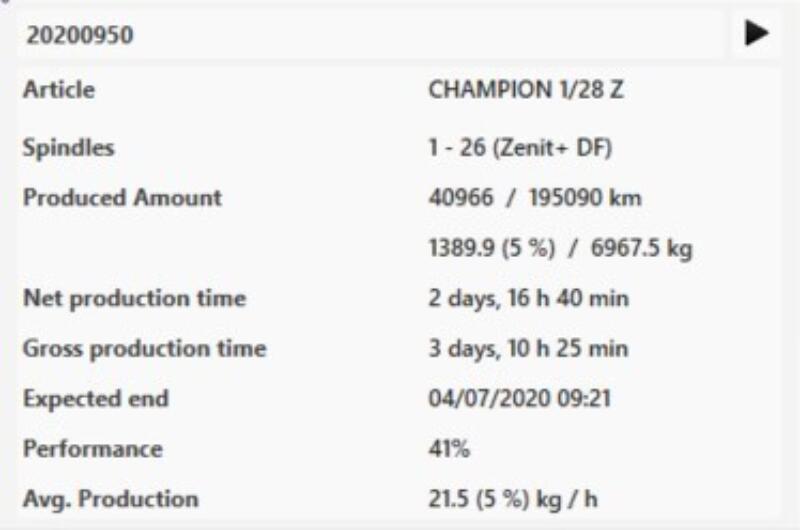
Proper resource planning can majorly influence the profitability of a spinning mill. This involves the demand-related ordering of raw materials, auxiliary materials and supplies, the planning of the individual orders and their throughput times, the corresponding allocation of machines per order, article and batch and the corresponding deployment of personnel.
The extensive planning required to ensure an efficient and smooth order processing is significantly simplified by MillMaster TOP’s "Planning Board". The "Planning Board" shows the following helpful information and features:
- the article/lot which is currently running on a machine
- the article/lot which is currently stopped or pausing
- the article/lot which is planned on a machine
- the date/time an article/lot will be completed
- the amount of an article/lot to be produced
- the amount of an article/lot already produced
- the efficiency with which an article/lot is produced
- the average production volume per hour
- warning if an article/lot cannot be completed on schedule
- display of waiting times for maintenance work
- automatic download of article/lot parameters to the winding machines’ control panels
Solutions & Benefits
With this wealth of information, a variety of measures can now be taken to optimize processes and reduce resources.
By using "Planning Board", customer orders (articles/lots) can be scheduled to the winding machines according to demand. Thanks to the reliable indication of when an article/lot will be finished, materials flow and personnel requirements can be optimized. The dispatcher can use “Planning Board” at any time to obtain information on what is being produced, where and how much - and when a customer order can be delivered. If an order is delayed, warning symbols are displayed to inform the scheduler.
MillMaster TOP’s "Planning Board" function enables winding machines to be used to their full capacity, thus positively influencing the spinning mill’s entire production flow. Consequently, production and personnel costs are also reduced.