Correct maintenance planning offers more than expected
Maintenance is a crucial part of any operation, but it can be demanding in terms of resources. It not only consumes significant time and money, but it can also have a direct impact on the quality of yarn produced. Therefore, it is of the utmost importance to plan and execute maintenance activities efficiently.
MillMaster TOP offers Lab Trend - a powerful analysis tool that provides a comprehensive evaluation of maintenance intervals, allowing for continuous improvement. This innovative feature not only guarantees top-notch yarn quality but also enhances the overall efficiency of winding machines.
By utilizing the Lab Trend feature, you can make informed decisions about when and how often maintenance should be performed. This data-driven approach ensures that maintenance activities are carried out at the most optimal intervals, preventing any unnecessary downtime or disruptions. Ultimately, this holistic approach to maintenance not only preserves yarn quality but also maximizes the productivity and profitability of your operations.
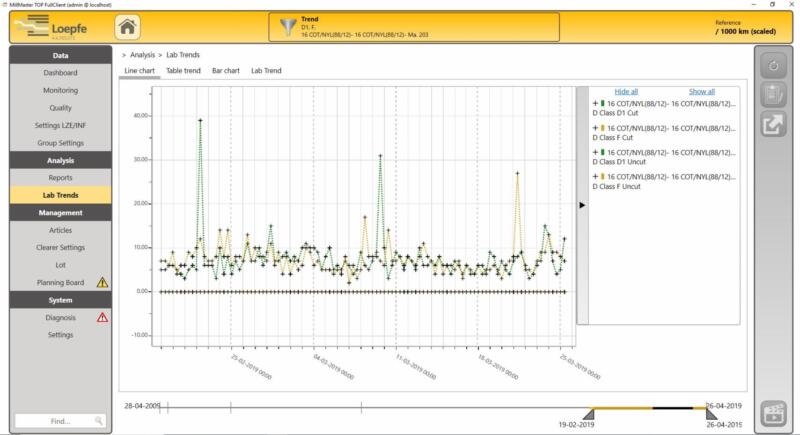
Optimizing maintenance intervals
Here is an example of how spinning mills can use Lab Trend analysis to effectively determine whether their maintenance intervals are being planned and carried out correctly. By analyzing this Lab Trend visualization, spinners can easily notice a periodic increase in events within the D1 and F classes on two specific winders. These machines have error peaks that are the multiple of the normal average.
Targeted measures
It is important to take immediate action to resolve the problem with the two winding machines and avoid such malfunctions in the future. To determine the cause of this error, operators can refer to Loepfe's “Classification of Yarn Faults and Their Sources” table, which helps quickly narrow down the possible causes for the increase of events.
Reasons for rising faults in the class D1 and F:
D1
- Drafting faults
- Break draft and roller setting selection in ring spinning frame
- Fluff accumulation in clearer roller in ring spinning frame
- Improper spacer selection in roving frame
- Improper twist selection in roving frame
F
- Improper cylinder to doffer transfer at carding
- Top arm load variation in draw frame
- Off-centered spindle on ring spinning frame
Based on the data presented in this list, it is evident that the significant increase in events can be attributed to a dirty drawing device in the ring frame. Furthermore, the repetitive peaks observed indicate that the cleaning interval at the ring-spinning machine should be reduced.
By proactively addressing the problem of the dirty drawing device and adjusting the cleaning intervals, it mitigates the occurrence of events and prevents any negative impact on yarn quality. Through this data-driven approach to maintenance, we can optimize production processes, minimize downtime, and ultimately achieve better results for our operations.