How to reduce cuts, yarn waste, splice cycles and energy consumption
PRISMA's Matrix Clearing is the perfect solution for spinners who want to reduce yarn waste and maximize raw material utilization. Loepfe’s matrix clearing is the foundation of easy and profitable production, putting the user at the center. The clearing matrix paves the most advanced way to optimize clearing limits. It has now been extended to the longest observation lengths on the market. Spinners can be sure that their production is optimized for maximum profitability.
Loepfe’s unique matrix clearing
PRISMA's matrices are designed to be intuitive and highly customizable. With its touch screen and visual settings, users can quickly and accurately adjust clearing curves to their exact specifications. PRISMA's software offers significant advantages over other systems in terms of speed, accuracy and flexibility, allowing users to get the best results in any situation. Its advanced features provides precise control over the clearing process.
- Classification of every deviation in absolute length
- Informs users about the actual fault deviation at different lengths and limits
- Provides data about the fault distribution and yarn structure even with an open setting
- Longest observation lengths on the market for the following fault types and matrices:
- OffCount (Deviations in Count) up to 50 m
- SFI/D (Hairiness and CV) up to 80 m
- OffColor (Deviations in Color) up to 50 m
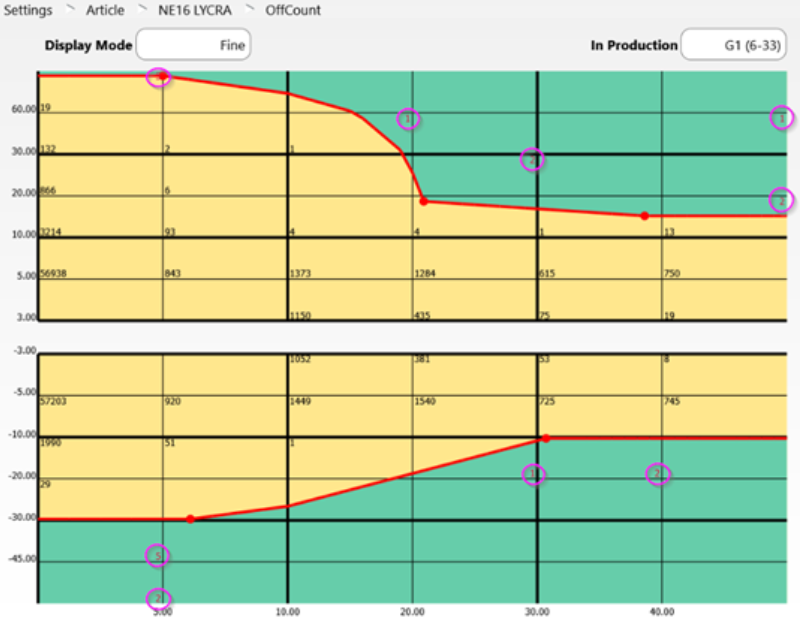
Benefits of the extended observation lengths
The extended observation length is the perfect solution for achieving higher-quality yarn with fewer cuts. PRISMA removes long faults in the yarn in a single cut and accurately identifies them, providing the most complete picture of the yarn structure in the process. Thanks to its extended observation length, spinning mills enjoy improved yarn quality, fewer splice cycles, and fewer cuts overall - all while saving time and money.
The matrix comes with multiple set points to provide the highest flexibility in setting the clearing curve to ensure the required fabric appearance.
The shorter observation lengths of conventional systems causes cuts immediately when the faults exceed the set curve. Slicing long faults into pieces will significantly downgrade the winding efficiency as well as cause more yarn waste. In addition, the fault is not assigned in its absolute length, which leads to a limited overview of the yarn. A missed opportunity for spinning process optimization.
Example Matrix clearing OffCount: Faults are classified with their absolute length (circled numbers in the green area)